Since we decided to get a little more serious about hatching chicks this year, we needed to increase our capacity. Chicks require a 21 day incubation period. We prefer to use an automatic turner in the incubator to eliminate the need to manually turn eggs 3-4 times a day. On day 18, you put the eggs on “lockdown” which means removing the turner and letting the eggs sit still until they hatch. While a basic still air incubator is made of styrofoam and doesn’t have a fan works fine for the entire cycle, it is actually limited to about 25 days. That’s because the nominal 21 day incubation results in some hatches out to about day 23. Then you have to clean it out, reload, etc.
For the initial part of the incubation period, the humidity is kept around 40%. From lockdown on, it needs to be around 75%. A limitation of the still air incubator is they don’t do well at trying to raise the humidity.
Our solution was to move the eggs to a different location to hatch. That means the incubator with automatic turner stays in operation. Now at day 18, eggs go into the hatcher and the incubator gets new eggs. Since we are running 2 incubators with turners, we have 41 eggs going to hatch every 9 days (once the cycle is in progress).
Here is our homemade chick hatcher. It has undergone a few different modifications, but I think the design has stabilized for a while.
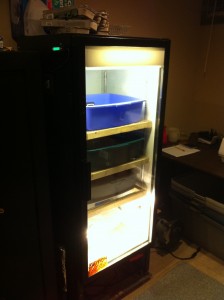
The hatcher is made from an old beer fridge I got from a bar (for free). The compressor was no good, so I removed the compressor and cooling coils.
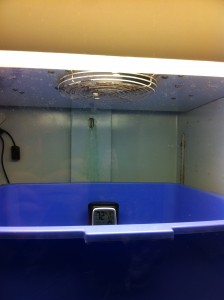
I reversed the polarity of the fan so it draws air up through the unit instead of blowing on the top shelf. I also added a rheostat to make it a variable speed fan.
I kept the fluorescent light so we can see the chicks hatching. Since the bar planned to reuse the shelves in a new unit, I made shelves out of 2x2s and wire mesh. Since I took these pictures, we did change to a basket setup instead of the cat litter boxes so the air circulates better.
I installed a floor air conditioning register in the side to allow for fresh air to enter the unit as the chicks hatch. The cables you see going in are for the digital thermostat and humidistat. You can see the small controller on the side in the first picture (it is blue). The digital controller was $70, but absolutely worth the improvement.
The heat source is a 125 Watt heat lamp that I wired into the bottom. We are using a humidifier in the bottom to keep the humidity in the appropriate range. The digital controller regulates the temperature within about 1 degree and the humidity within about 5%.
The total cost of materials was about $100 and the end result is a hatcher that gives up plenty of room to increase production in the future and we got an 80% hatch rate out of our last batch of eggs. Using a still air incubator, our best ever was about 60%.